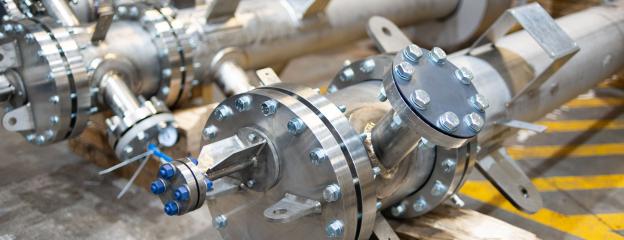
Custom built products
Over 7 decades, Welders N.V. has gained an extensive engineering expertise and fabrication know-how in high-integrity custom-built process equipment in heat- and corrosion resistant alloys used in numerous applications.
Welders’ Design and Engineering Department operates a comprehensive system, using software of international repute for thermal rating, stress analysis, wind load and seismic resistance calculations, as applicable. Combined with our expertise, it enables Welders’ engineers to optimise the equipment sizing and configuration and to maximize its cost-effectiveness.
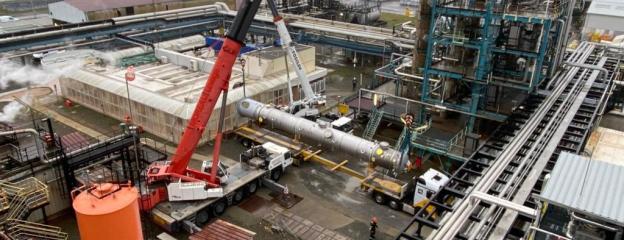
Industries served
The equipment constructed by Welders N.V. is used in numerous applications, particularly in the hydrocarbon and downstream industries, but also in other industries featuring aggressive atmospheres or operating in environments calling for heat or corrosion resistant materials.